Long Radius Bends - Hot Bend
Top Quality Manufacturer and Stockist of Hot Bends
Citizen Pipe Fittings offers Hot Bends at Best Price
Citizen Pipe Fittings a renowned name in the industry, offers superior quality Hot Bends, also known as Induction Bends. These bends are manufactured using an advanced induction bending process, which involves local heating with high-frequency induced electrical power. This process ensures precision and consistency in every bend
Citizen Pipe Fittings’ Hot Bends are designed to provide efficient direction changes in pipelines, adding flexibility to the piping systems. They adhere to the American standard ASME B16.49, ensuring high standards of quality and safety. These Hot Bends find extensive application in the oil and gas industries, among others, due to their durability and reliability. With a variety of bend radii options like 5D, 30D, 60D, etc., they cater to diverse industrial needs
Citizen Pipe Fittings’ commitment to quality and customer satisfaction makes their Hot Bends a preferred choice for various industrial applications. Experience the difference with Citizen Pipe Fittings’ Hot Bends – where quality meets precision
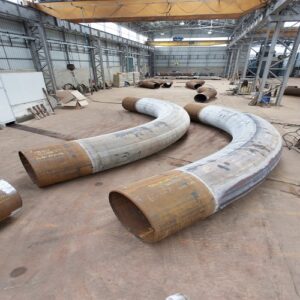
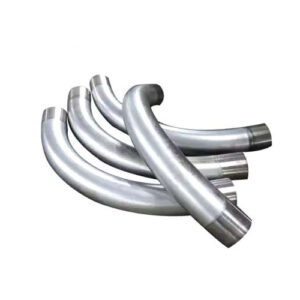
Types of Hot Bends
Hot bends, often used in various industries such as construction, automotive, and aerospace, are tailored to meet specific requirements. Here are some types of hot bends
- 90-Degree Bends : These are the most common type of bends, used in a variety of applications. They are designed to change the direction of a pipe or tube by 90 degrees
- 45-Degree Bends : These bends are used when a more gradual change in direction is needed. They are often used in plumbing and irrigation systems
- U-Bends : U-bends are used to redirect the flow of a pipe or tube in the opposite direction. They are commonly used in heat exchangers and exhaust systems
- J-Bends : These are similar to U-bends but have one leg longer than the other. They are often used in automotive exhaust systems
- Offset Bends : Offset bends are used to navigate around obstacles while maintaining the same direction of flow
- Cross Bends : Cross bends are used to split the flow of a pipe or tube into two different directions
- Reducer Bends : These bends are used to change the diameter of the pipe or tube, in addition to changing its direction
- Compound Bends : Compound bends consist of two or more bend angles in a single piece. They are used in complex systems where multiple direction changes are required
Key Features of Hot Bends
Hot bends, as the name suggests, are created using a process that involves heating. Here are some key features of hot bends- High Flexibility : Hot bends offer a high degree of flexibility in terms of the bend angle and radius, making them suitable for a wide range of applications
- Strength : The process of hot bending strengthens the material, making the bends more durable and resistant to wear and tear
- Smooth Surface : Hot bends typically have a smooth surface, which reduces friction and allows for a more efficient flow of materials
- Wide Material Compatibility : Hot bending can be used with a variety of materials, including metals and plastics
- Cost-Effective : While the initial cost of hot bending may be higher due to the equipment and energy required, the long-term benefits in terms of durability and efficiency can make it a cost-effective choice
- Reduced Stress : The process of hot bending reduces the internal stress in the material, which can improve its overall performance and lifespan
Applications
Hot bends are utilized in a variety of industries due to their unique properties and the advantages they offer. Here are some applications of hot bends :
- Pipelines : In the oil and gas industry, hot bends are used in the construction of pipelines. The high flexibility and strength of hot bends make them ideal for this application
- Automotive : Hot bends are used in the manufacturing of various automotive parts, including exhaust systems and engine components. Their durability and smooth surface contribute to improved vehicle performance
- Construction : In the construction industry, hot bends are used in structural applications, such as the construction of bridges and buildings. Their strength and reduced internal stress make them suitable for these applications
- Aerospace : In the aerospace industry, hot bends are used in the manufacturing of aircraft components. The high strength-to-weight ratio of hot bends is particularly beneficial in this field
- Manufacturing : In various manufacturing processes, hot long radius bends are used in the production of machinery and equipment. Their wide material compatibility and cost-effectiveness make them a popular choice
Specifications
Specification | Details |
---|---|
Pipe Diameter (O.D) | min. 2” (60,3 mm); max 60” (1524 mm) |
Seamless Bend | (1/2″- 24″) |
ERW / Fabricated/ Welded Bend | (2″- 36″) |
Radius | min. 100 mm; max. 11000 mm |
Wall thickness | max. 200 mm |
Hot Bend Heating system | max. 1030 KW |
Bending capability | 15,000 metric tons per year |
Wall Thickness | 3mm- 40mm / SCH5, SCH10, SCH20, SCH30, SCH40, STD, SCH80, XS, SCH60, SCH80, SCH120, SCH140, SCH160, XXS |
Pipe Bend Radius | R=1D, 2D, 3D, 5D, 6D, 8D, 10D or Custom |
Straight Length | L 300mm and 1500mm |
Pipe Bend Angle | 0°- 180° |
Grades
Material | Grade |
---|---|
Stainless Steel | ASTM A403 WP316/316L, ASTM A403 WP304/304L, ASTM A182 F316L, 304L, DIN 1.4301, DIN1.4306, DIN 1.4401, DIN 1.4404 |
Carbon Steel | ASTM A 234 WPB, WPBW, WPHY 42, WPHY 46, WPHY 52, WPH 60, WPHY 65 & WPHY 70 |
Alloy Steel | ASTM / ASME A/SA 234 Gr. WP 1, WP 5, WP 9, WP 11, WP 12, WP 22, WP 91 |
Nickel Alloy | ASTM / ASME SB 336 UNS 2200 (NICKEL 200), UNS 2201 (NICKEL 201), UNS 4400 (MONEL 400), UNS 8020 (ALLOY 20 / 20 CB 3), UNS 8825 INCONEL (825), UNS 6600 (INCONEL 600), UNS 6601 (INCONEL 601), UNS 6625 (INCONEL 625), UNS 10276 (HASTELLOY C 276) |
Duplex & Super Duplex | ASTM A 815, ASME SA 815 UNS NO S31803, S32205 |