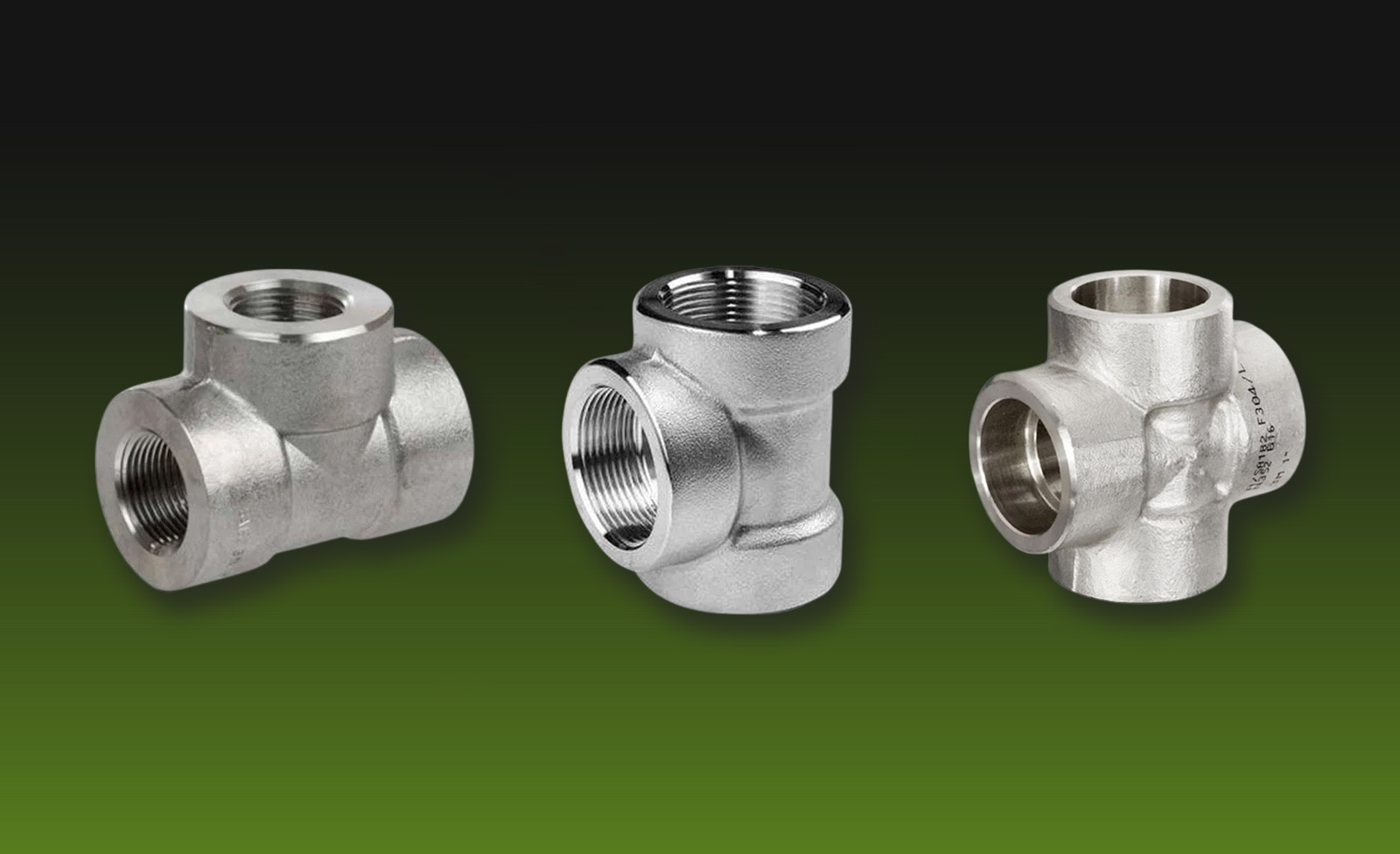
What are Forged Fittings and how are they produced
Forged fittings are pipe fittings made from forged materials. Forging is a manufacturing process where a piece of metal is heated to a high temperature and then shaped by applying force or pressure. This process alters the grain structure of the metal, enhancing its mechanical properties such as strength and durability
The process of making forged fittings involves several steps :
- Heating : The raw material, usually a billet of steel or other metal, is heated until it becomes malleable. This is done in a furnace
- Forging : The heated material is then placed under a high-pressure forging press, which applies force to shape the metal into the desired form. This could be a tee, elbow, coupling, or any other type of pipe fitting
- Trimming : After forging, the excess material is trimmed off to give the fitting its final shape
- Heat Treatment : The forged fitting is then heat-treated to enhance its mechanical properties. This usually involves processes like normalizing, quenching, and tempering
- Machining : The fitting is then machined to its final dimensions and specifications. This could involve processes like drilling, threading, or surface finishing
- Inspection and Testing : Finally, the forged fitting is inspected and tested to ensure it meets all necessary standards and specifications
Why Forged Fittings are preferred for High-Pressure Applications
Forged fittings are known for their exceptional strength. The forging process aligns the grain structure of the metal along the shape of the fitting, which significantly enhances its tensile strength and resistance to stress. This makes them capable of withstanding high pressure without deformation or failure
Forged fittings are highly durable. The high-temperature forging process results in fittings that are resistant to impact, shock, and wear. This means they can maintain their structural integrity even under harsh conditions, making them ideal for long-term use in high-pressure systems
The reliability of forged fittings is another key factor. The rigorous manufacturing process, which includes heat treatment and thorough testing, ensures that each fitting meets the highest quality standards. This means you can trust them to perform consistently and safely, even in critical high-pressure applications
High-Pressure Applications of Forged Fittings
- Oil and Gas Industry : The oil and gas industry is one of the primary sectors where forged fittings are extensively used. These fittings are used in both upstream (exploration and production) and downstream (refining and distribution) operations. They are used in pipelines, drilling rigs, and processing facilities where they have to withstand high pressures and corrosive environments
- Power Plants : Forged fittings are crucial components in power plants, especially in nuclear and thermal power stations. They are used in various systems such as steam generation, cooling, and fuel handling. The high-pressure steam lines in these plants particularly require the strength and durability of forged fittings
- Chemical Industry : The chemical industry uses forged fittings in their processing plants. These fittings are used in piping systems that carry high-pressure fluids, gases, and corrosive substances. The ability of forged fittings to resist chemical corrosion makes them ideal for this industry
- Marine Applications : Forged fittings are used in various marine applications, including shipbuilding and offshore platforms. They are used in high-pressure hydraulic systems, fuel lines, and other critical systems on board
- Mining Industry : In the mining industry, forged fittings are used in high-pressure applications like pneumatic drilling and hydraulic systems for machinery
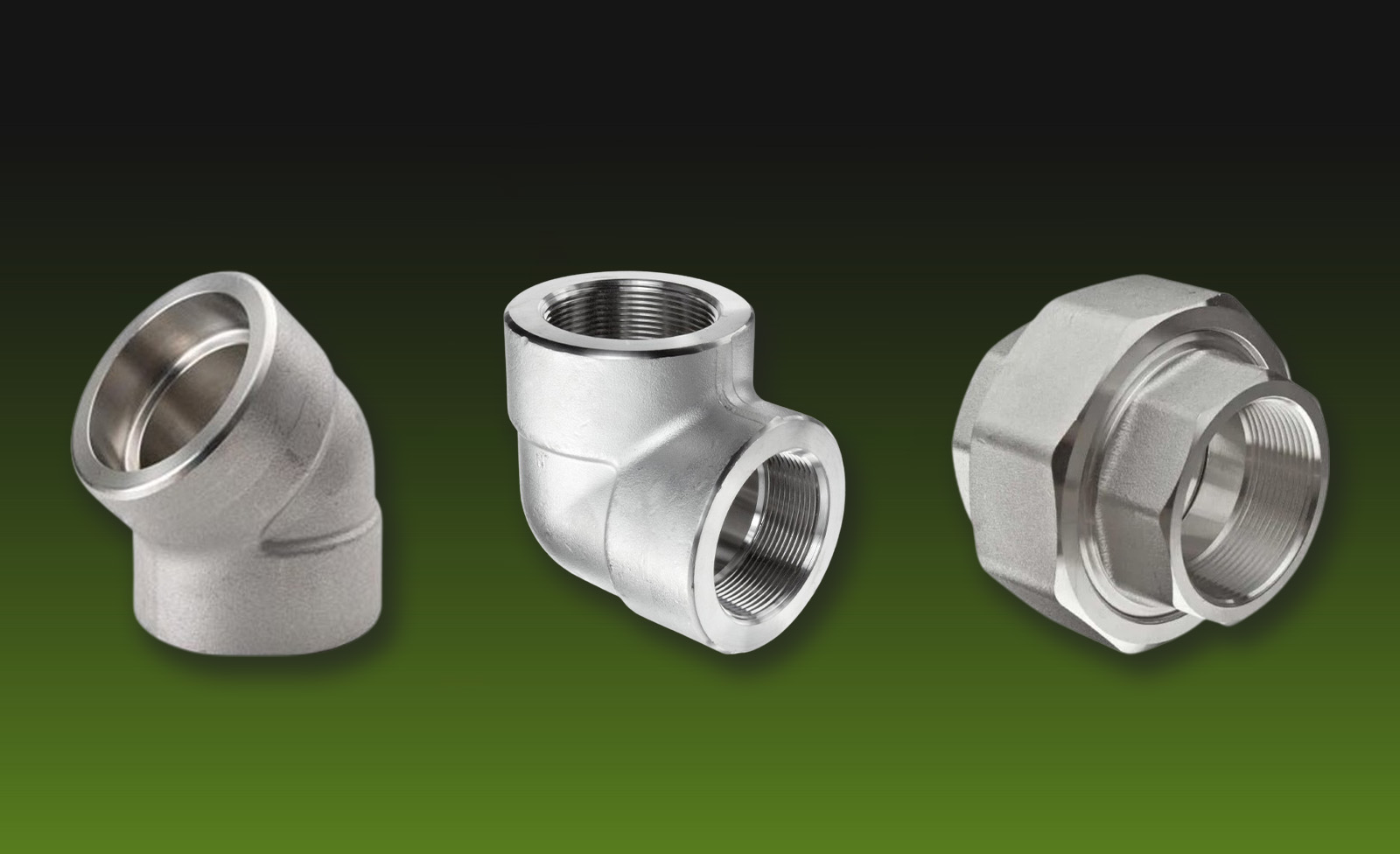
Factors to consider when selecting forged fittings for high-pressure applications
- Material Type : The material of the fitting is crucial as it needs to withstand high pressure. Materials like stainless steel, carbon steel, and alloy steel are commonly used due to their strength and durability
- Pressure Rating : It indicates the maximum pressure it can handle. It's essential to choose a fitting with a pressure rating higher than the application's maximum pressure to ensure safety and reliability
- Size : The size of the fitting should match the size of the pipe it's connecting. An incorrect size can lead to leaks or even failure of the system
- Application Requirements : The specific requirements of the application also play a role in the selection. For instance, certain applications may require fittings that can withstand high temperatures, while others may need corrosion-resistant materials
How the wrong choice of Fittings can lead to failures and potential hazards in High-Pressure applications
In high-pressure applications, the selection of appropriate fittings is crucial. The wrong choice can lead to a variety of failures and potential hazards. Here’s how
- Leakage : Improperly sized or type of fittings can cause leaks, leading to equipment malfunction and safety hazards
- Bursting : Fittings not rated for system pressure may burst, causing system damage and potential injuries
- Material Incompatibility : Incompatible fitting materials can corrode, weakening the fitting and increasing failure likelihood
- System Failure : A single failure can trigger a cascading system failure due to a sudden pressure drop
- Environmental Impact : Fitting failures in systems carrying hazardous materials can cause environmental harm
- Financial Loss : Fitting failures can cause costly system downtime, cleanup, repairs, and component replacement
Tips or guidelines on how to choose the right Forged Fittings
Choosing the right forged fittings for your application is crucial to ensure safety, efficiency, and longevity. Here are some tips and guidelines to help you make the right choice
- Understand Your Application : Know your application including the type of fluid, operating pressure and temperature, and environmental conditions
- Choose the Right Material : Select from materials like stainless steel, carbon steel, and alloy steel based on your application
- Consider the Pressure Rating : Choose a fitting with a pressure rating exceeding your application’s maximum pressure
- Select the Appropriate Size : Ensure the fitting size matches the pipe’s diameter and wall thickness
- Check for Industry Standards : Choose fittings that comply with any standards applicable to your industry
- Consider the Manufacturer : Opt for manufacturers known for quality, reliability, and good customer service
- Plan for Maintenance : Choose easily replaceable and readily available fittings to minimize downtime
Citizen Pipe Fittings, a leading manufacturer and exporter of forged fittings, have proven to be an indispensable solution in high-pressure applications. The robust construction, achieved through the forging process, ensures exceptional durability and resistance to extreme pressure conditions. This makes us an ideal choice for industries where high-pressure systems are a norm. Furthermore, the reliability and performance of these fittings contribute to operational efficiency and safety, reinforcing their value in such demanding environments