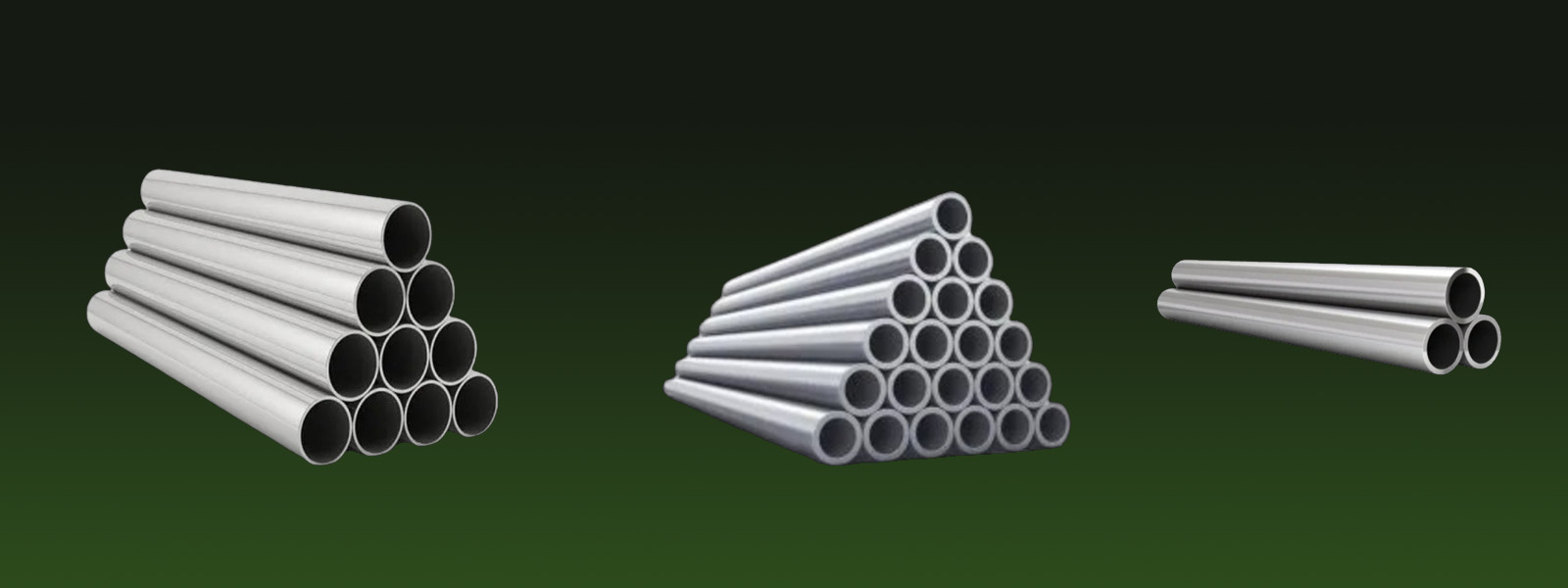
When it comes to industries that require high strength, exceptional corrosion resistance, and durability, Duplex steel seamless pipes are often the go-to choice. These pipes are indispensable in various sectors, including chemical processing, oil and gas, marine engineering, and more. But what exactly are these pipes made of, and why are they so revered in demanding applications? Let’s dive deeper into the composition and characteristics of duplex steel, the material behind these robust pipes
Understanding Duplex Steel
Duplex steel is therefore a stainless steel that has a two-phase structure that is made up of both the austenite and ferrite phases. This special combination is responsible for the mechanical properties of the duplex steel. The combination of these two phases normally produces a material that is more tough and resistant to stress corrosion cracking than both the austenitic and ferritic stainless steels
The austenitic phase of the material provides good ductility and toughness to the material and the ability to cope with high pressure conditions without getting distorted makes the material suitable for use in seamless pipes. On the other hand, the ferritic phase improves corrosion resistance, especially in conditions where there are chloride ions such as in seawater or chemical plants. This arrangement of phases is what makes duplex steel a material of preference for pipes that are to be used in extreme conditions
Composition of Duplex Steel
The primary elements in duplex steel include chromium, nickel, and molybdenum, but what makes duplex steel unique is the balance between these elements and the addition of nitrogen. Here’s a breakdown of the key components
- Chromium (Cr) : Duplex steel has a chromium content of between 22% and 26%. This high chromium content is essential for the formation of a passive layer on the surface of the steel, which will reduce the chances of corrosion. This is the characteristic that makes the duplex steel to be resistant to oxidation and general corrosion.
- Nickel (Ni) : Nickel content is slightly lower than in austenitic stainless steels and ranges from 4. 5-6. 5%. The nickel content is used to stabilize the austenitic phase which is responsible for the ductility and toughness of the material.
- Molybdenum (Mo) : Normally, the molybdenum content of the duplex steel is in the range of 3-5% which provides it with additional protection against pitting and crevice corrosion particularly in chloride-containing solutions.
- Nitrogen (N) : The inclusion of nitrogen is another feature of duplex steel, which usually constitutes about 0. 08-0. 2% of its composition. Nitrogen enhances the mechanical properties of the material and aids in stabilising the austenitic phase, thus enhancing the general corrosion resistance.
- Other Elements : Manganese, silicon and carbon may also be present in small proportions in the composition of the duplex steel to enable it to have the right mechanical properties as well as the right resistance to corrosion
The Making of Duplex Steel Seamless Pipes
The process of creating Duplex steel seamless pipes is meticulous and requires precise control over the material’s composition and structure. Here’s a brief overview of how these pipes are made
- Melting and Casting : The process starts with the melting of the raw materials which include iron ore, scrap metals and the alloying elements mentioned above in an electric furnace. This molten metal is then poured into an ingot, billet or slab.
- Hot Working : The cast billets are then heated and rolled to the required shape and dimensions of the pipe as required. In this stage, the material is deformed and this increases the mechanical properties of the material.
- Piercing : In seamless pipes, the billet is pierced to form a hollow tube. This is done by means of a mandrel or plug, which is forced into the hot billet to create the pipe’s inside diameter.
- Cold Working : The pipes after piercing may be subjected to cold working processes including drawing or pilgering to the required dimensions and surface finish. Cold working also enhances the strength and hardness of the material as a result of the deformation that occurs in the material.
- Heat Treatment : In order to attain the duplex structure, the pipes are exposed to solution annealing in which the pipes are heated to a certain temperature and quenched. This step is necessary in order to achieve the balanced austenitic-ferritic structure which is characteristic for the duplex steels.
- Quality Control : Last but not least, the Duplex steel seamless pipes are subjected to various tests such as ultrasonic testing, hydrostatic testing, and chemical testing to meet the standards and requirements of the industry
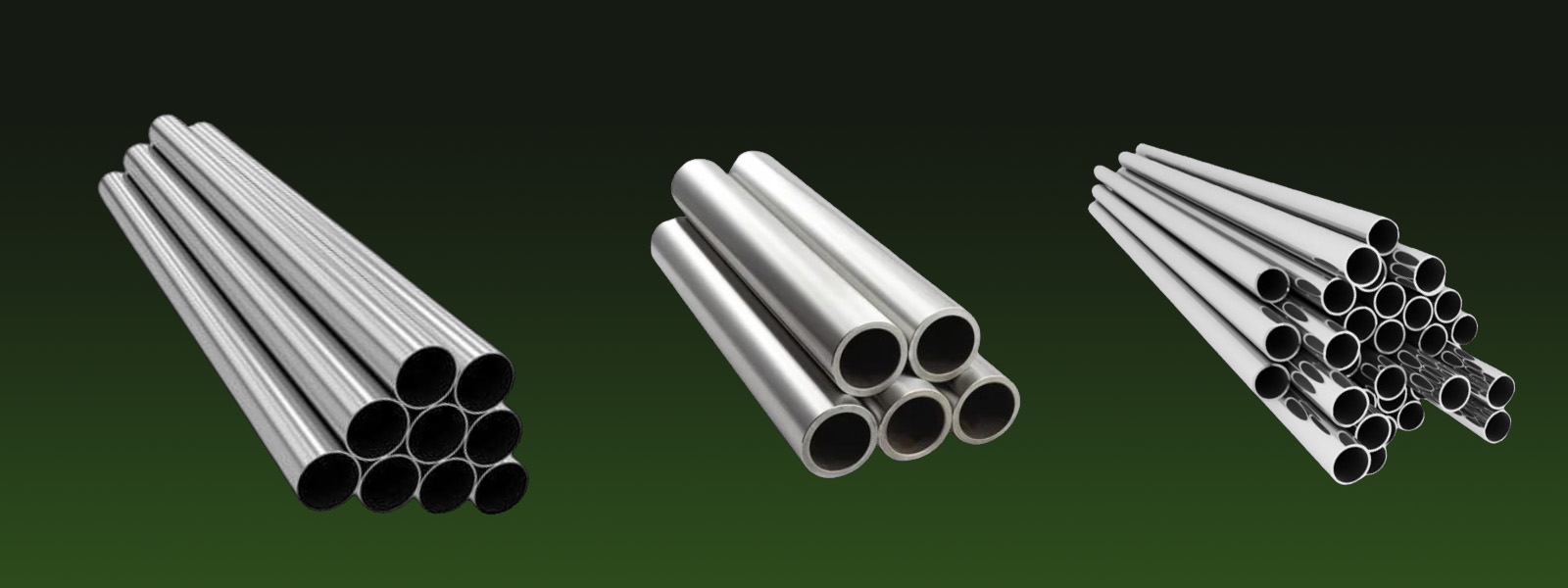
Types of Duplex Steel Used in Seamless Pipes
Duplex steel, a combination of austenitic and ferritic stainless steels, offers excellent corrosion resistance, high strength, and durability, making it suitable for use in harsh environments like oil and gas or chemical industries. Its different types—Standard Duplex, Super Duplex, Lean Duplex, Hyper Duplex, and 2507 Duplex—each offer unique properties for various industrial applications
- Standard Duplex (UNS S31803/S32205) contains around 22% chromium, 5-6% nickel, and 3% molybdenum, offering good resistance to stress corrosion cracking and pitting, along with high tensile strength, making it suitable for chemical processing and oil pipelines. Super Duplex (UNS S32750/S32760), with 25% chromium, 7% nickel, and 4% molybdenum, provides even greater corrosion resistance, particularly in harsh marine environments, and is often used in offshore platforms and subsea equipment.
- Lean Duplex (UNS S32304) with lower nickel and molybdenum content (around 22% chromium, 4-5% nickel, and 0.1-0.3% molybdenum), is a cost-effective option that still offers good corrosion resistance and strength, making it suitable for less demanding environments like structural components and storage tanks. Hyper Duplex (UNS S32707/S33207), containing 27% chromium, 7% nickel, 3.5% molybdenum, and higher nitrogen, is designed for the most extreme conditions, offering superior corrosion resistance and strength, particularly in chemical processing and seawater handling.
- Finally, 2507 Duplex (UNS S32750), with 25% chromium, 7% nickel, 4% molybdenum, and 0.3% nitrogen, excels in chloride stress corrosion cracking and pitting resistance, making it ideal for desalination plants, heat exchangers, and high-pressure systems
Why Choose Duplex Steel Seamless Pipes?
When choosing pipes for critical applications, it’s important to consider the long-term benefits. Duplex steel seamless pipes offer a combination of strength, corrosion resistance, and durability that few other materials can match. Whether you are dealing with high pressure, corrosive environments, or extreme temperatures, these pipes are engineered to perform and outlast their counterparts
As a leading Duplex steel seamless pipes manufacturer and Duplex steel seamless pipes exporter, Citizen Pipe Fittings is committed to providing top-quality products that meet the highest standards. Our pipes are crafted with precision, ensuring they deliver reliable performance in the most demanding conditions
Conclusion
Duplex steel seamless pipes are made from a carefully balanced mix of chromium, nickel, molybdenum, and nitrogen, resulting in a material that combines the best attributes of austenitic and ferritic stainless steels. Whether for industrial, marine, or chemical applications, these pipes offer unparalleled strength and corrosion resistance, making them the preferred choice for industries worldwide
You can Contact Citizen Pipe Fittings at sales@citizenpipefittings.com to know more about Duplex Steel Seamless Pipe and their applications in various industries.